The case and need for mass timber
After more than a decade of hard work to unlock and demonstrate the potential for mass timber in Canada, the industry is ready to scale.
Almost 700 mass timber buildings have been completed in Canada, with more than 140 projects under construction or in planning stages. Canada has excellent wood resources and expertise all along the supply chain. Demand for mass timber beams, panels, and buildings is strong and growing.
The industry is advancing rapidly, but there is work to do to realize this opportunity of increasing manufacturing value-added products to the forest sector.
Mass timber presents a unique opportunity because it can help meet three critical needs in Canada:
» support the drive to net-zero buildings;
» help address the housing crisis; and
» create good jobs in rural and Indigenous communities.
Support net-zero buildings
Mass timber helps to reduce the carbon intensity of construction by eliminating concrete and steel emissions and by providing long-term carbon storage. Using wood products alongside other cost-effective decisions can reduce embodied carbon by as much as 40%. Since embodied carbon in materials represents the majority of lifecycle emissions from the construction of buildings, mass timber can have a huge impact.
Address the housing crisis
Mass timber can also help address Canada’s housing crisis.
Mass timber made its name in “tall wood” buildings and showpiece nonresidential buildings. Many of these buildings were “one-off” designs. But now, mass timber is primed to become a mainstream material of choice in residential applications, especially the 4-6 storey range and more common 7-12 storey buildings, including hybrid structures, combining wood with steel and concrete.
Mass timber designs, especially those incorporating prefabrication and modular approaches, offer a promising strategy to accelerate the construction of multi-unit residential structures, at greater speeds and lower costs. Mass timber panels, particularly cross-laminated timber, create opportunities for prefabrication because it allows entire wall assemblies to be manufactured and customized offsite. Window and door openings can be pre-cut and standardized connections can be used to assemble components quickly. These elements of prefabrication can be used to create highly customizable buildings. Mass timber can shorten construction times by as much as 20%. This lowers constructions costs (and financing costs), which are a major part of a building’s lifetime cost. Prefabrication and modularization could drive costs even lower.
Create good jobs in rural and Indigenous communities
Additionally, mass timber will create good jobs in rural and Indigenous communities. These communities have to see themselves as part of the net-zero transition. Too often, Canada’s resource communities feel left out of the future economy.
Mass timber can help bring them back in.
Forest to buildings value chains: A global race
As a result, countries are in a race to seize these benefits and the economic opportunities mass timber provides in the transition to a net-zero world.
Countries are using industrial policies to position their firms in rapidly forming global value chains. Critical to this competition are efforts to capture manufacturing value-added products: transforming primary resources into high value products that incorporate innovative technologies and advanced skills. Manufacturing is critical to long-term economic success because it can increase productivity and drive growth.
At the moment, Canada is falling behind in this race: many mass timber projects in Canada source mass timber products, such as CLT panels, from Europe rather than Canadian manufacturers. To compete globally, Canada needs to create an efficient, integrated forest-to-buildings value chain.
Time is of the essence. The country needs net-zero building solutions and the green jobs a rapidly growing mass timber industry will bring to forestry communities.
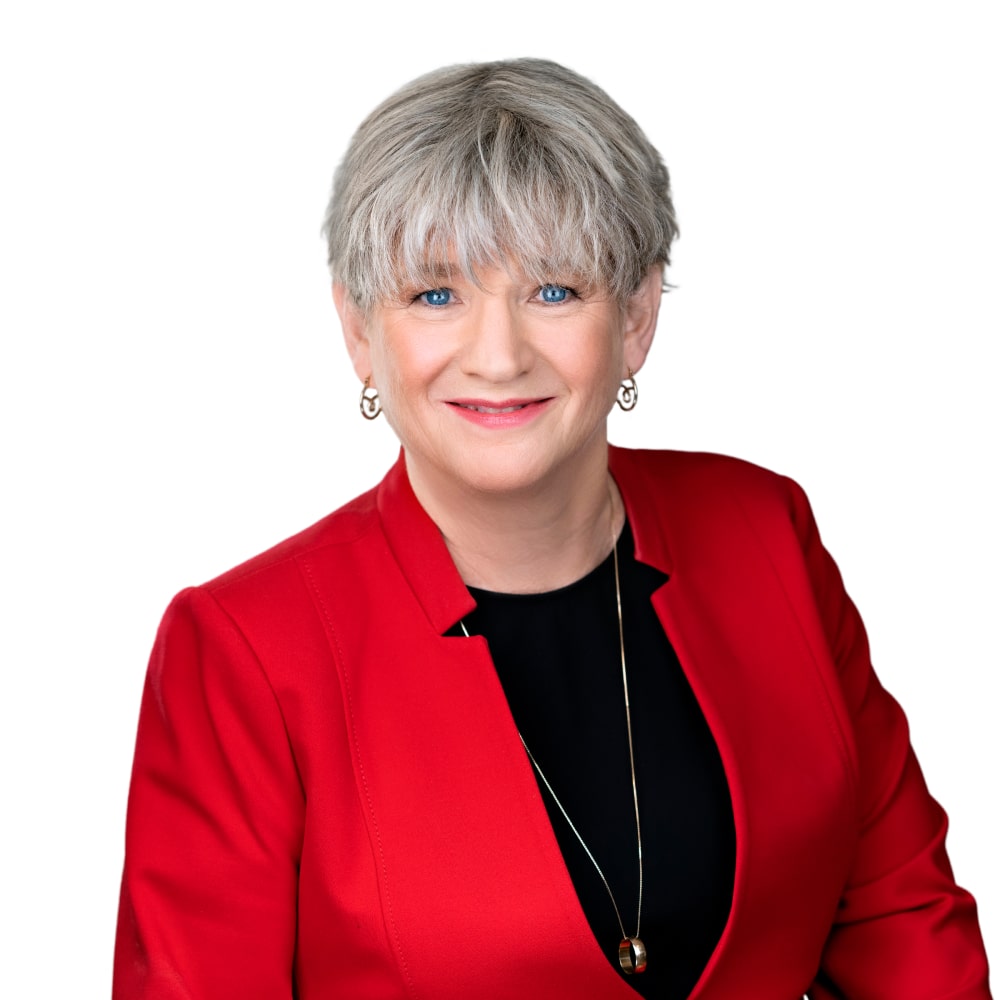