A standard manufacturing process consists of three inventory stages: RAW (Raw), WIP (Work In Progress), and FG (Finished Good). In sawmilling, the RAW goods would be the logs. The process of sawing a log into cants and dimensional boards, kiln drying, and planing would be WIP, including byproducts (chips and hog). Lastly, FG would be the finished lumber. Let’s dive into this some more.
RAW
Once logs arrive on the mill site, they are first weighed and then stored in the log yard. From there, logs are placed on the log infeed deck with a grapple loader where they enter the sawmill primary breakdown. Logs are then run through a cut-to-length merchandiser. A merchandiser is a series of circular saws that are driven by photo-eye optimizers, scanning whether the log needs to be trimmed down to a proper length. Once trimmed to length, if need be, the logs are run through a ring debarker where the bark is peeled off the log. These debarked logs are then run up a step feeder, allowing logs to be individually run through a bandsaw where sideboards are cut, and cants are sent further into production.
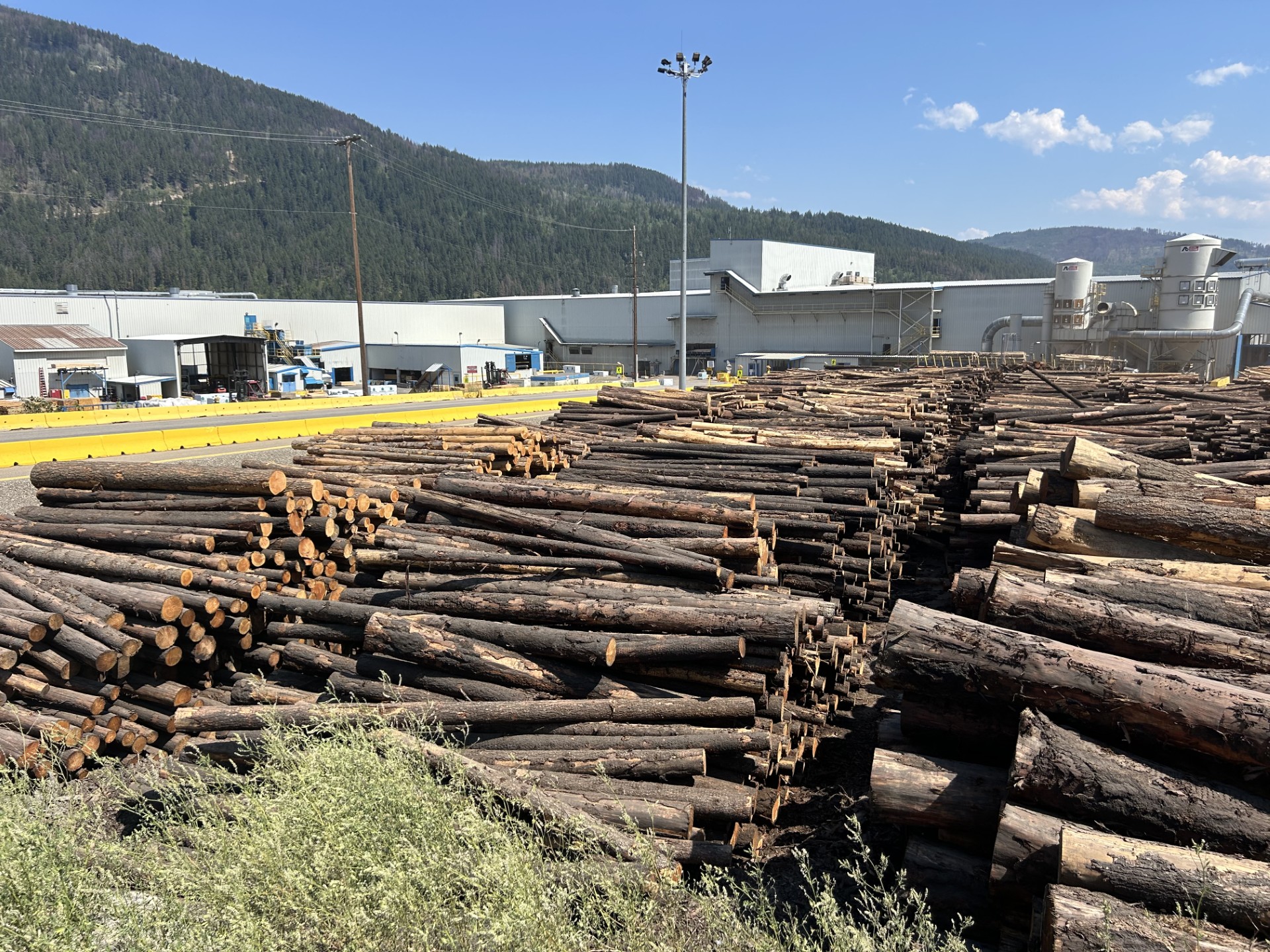
WIP
When a bandsaw runs through a log, the sideboards that are cut are kicked on to a chain-driven landing deck, where they move to a machine center called an edger. The edger is a series of vertical circular saws that move horizontally to cut that sideboard into a dimensional board, alleviating the wane. Sideboards are typically small-dimension boards, such as 1x4 and 2x4. At the same time, the center cant of such a log moves to the machine center called a VDA. A VDA is a series of horizontal saws that move vertically, cutting that cant into multiple boards. These are the larger boards: 2x4, 2x6, 2x8, and 2x10. All while this is occurring, oversize slabs are sent to the resaw. The resaw is a series of vertical saws that cut the oversize slab into smaller slabs that can then be kicked to the edger. After the VDA, boards are sorted at a machine center called a prime sort. At the prime sort, boards are either sent further into production if they are of spec, sent to the edger if wane still needs to be removed, or to the chipper if they are not capable of recovering a board. At the last machine center prior to entering sorter bins, where they will then go to the kilns, they are run through the trimmer. The trimmer is a series of circular saws called trim saws. At this station, the boards are trimmed to the proper length and/or trimmed to remove unfinished ends, wane, shake, and checks. Boards are then dropped into the mentioned sorter bins, depending on size, length, and moisture content. From here, they will be stacked and then picked up by a forklift from the outfeed and brought to a kiln infeed. Kilns are essentially big ovens. In the kilns, the lumber is run on tracks, moving slowly through the oven to dry at a certain temperature, humidity, and steam level. Turning the lumber from MRG (Machine Run Green) to KD (Kiln Dried). The last stage before being sent to the yard and being ready for shipment is the planer. The planer mill is a station where the boards are finished and dressed. Here, the boards are planed to their ultimate size and appearance.
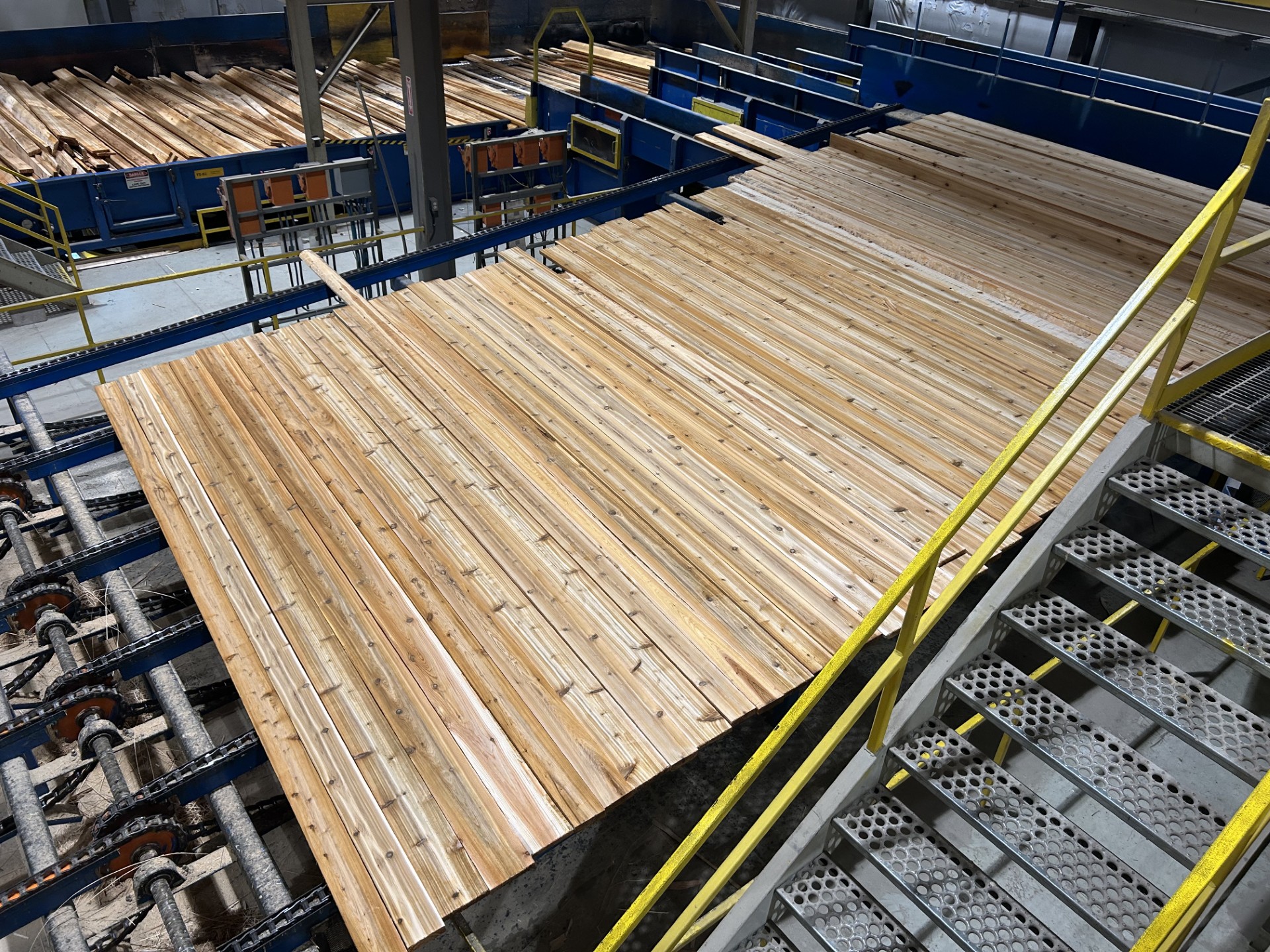
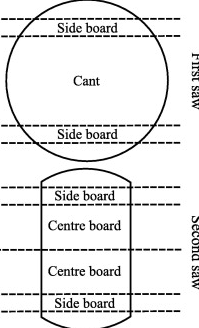
FG
The finished good stage consists of your finished product. This would be the bander station where the boards are wrapped and tagged, as well as the yards where lumber is stored and trucks are loaded for shipment.
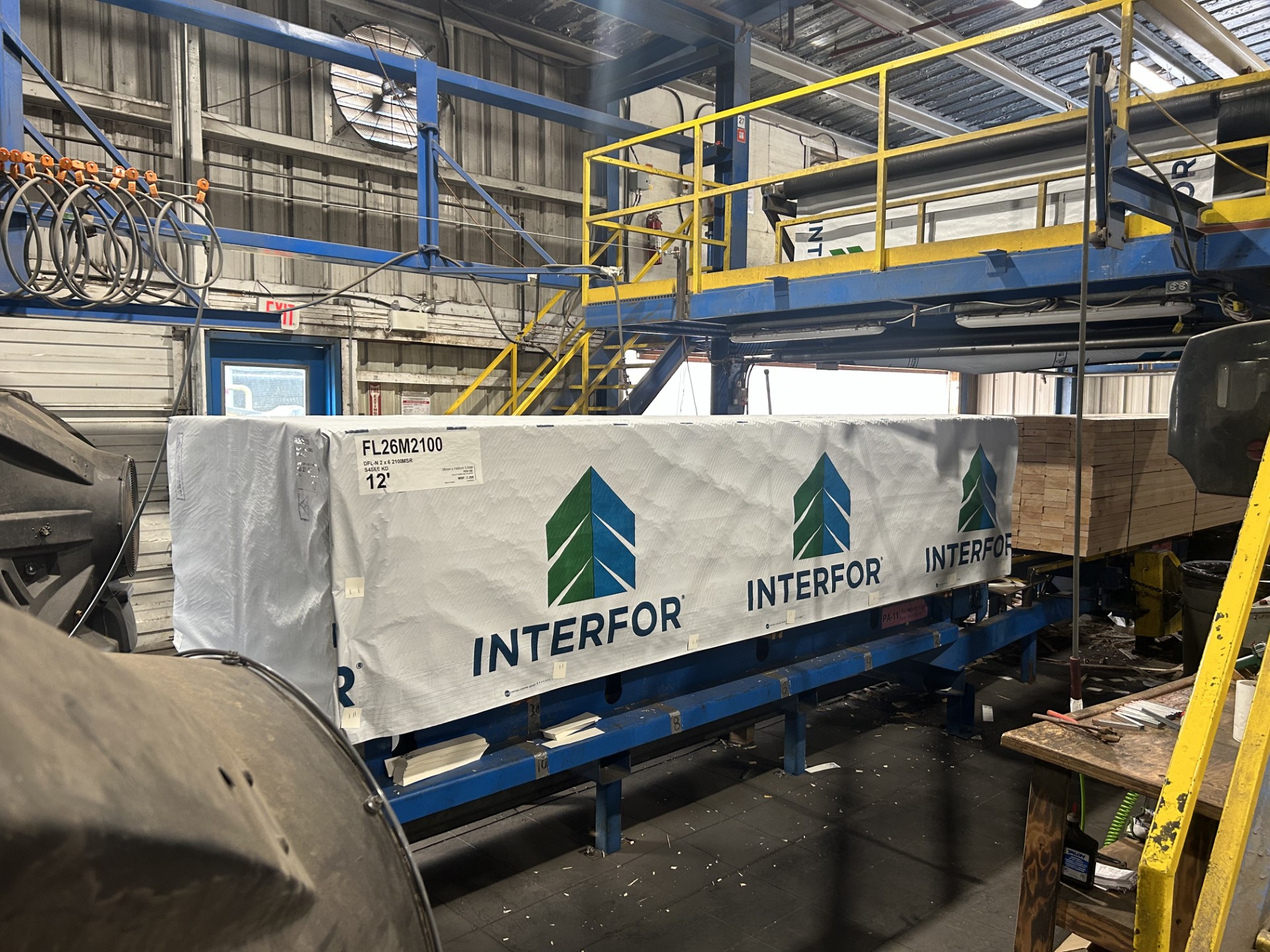
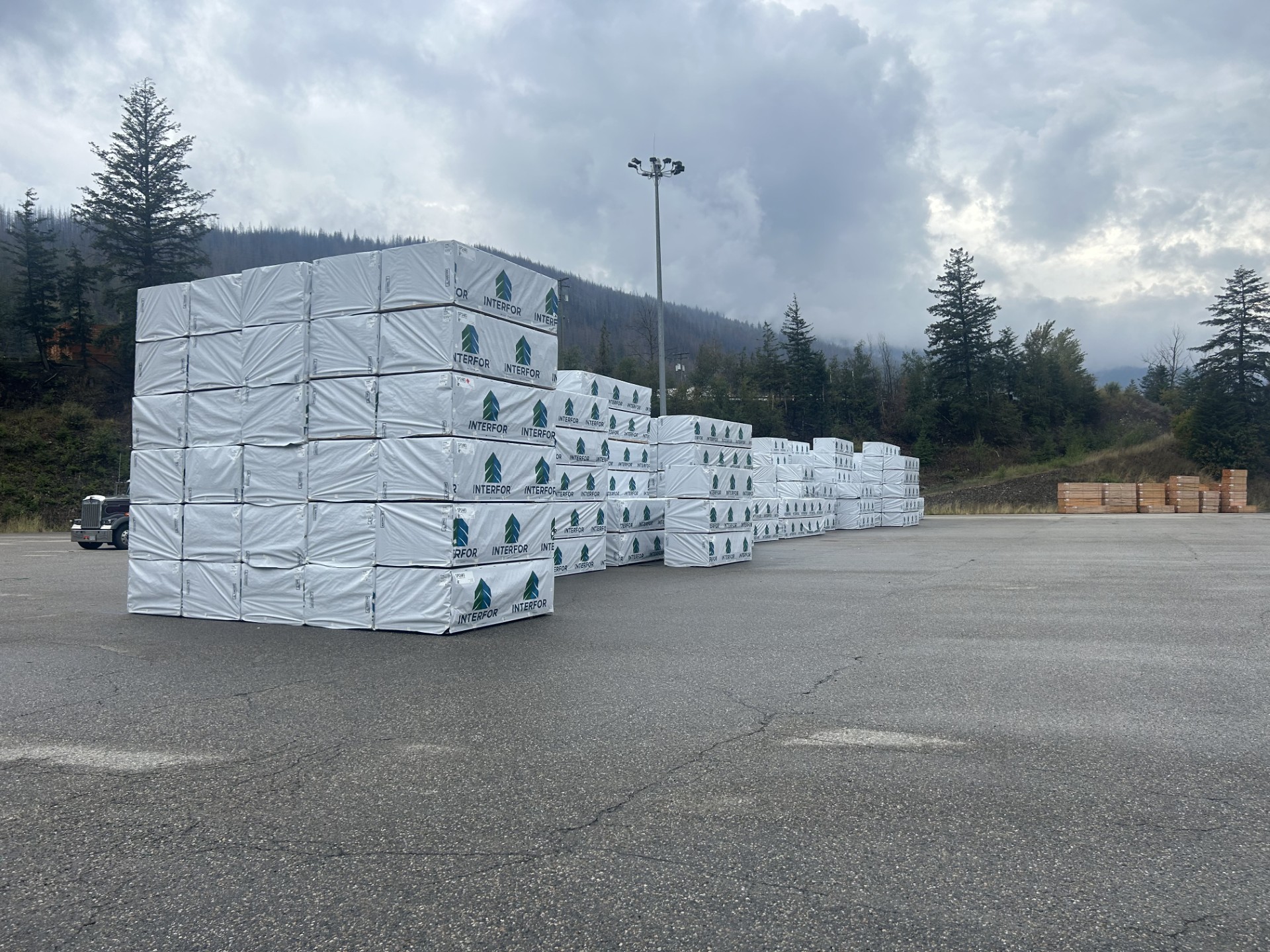
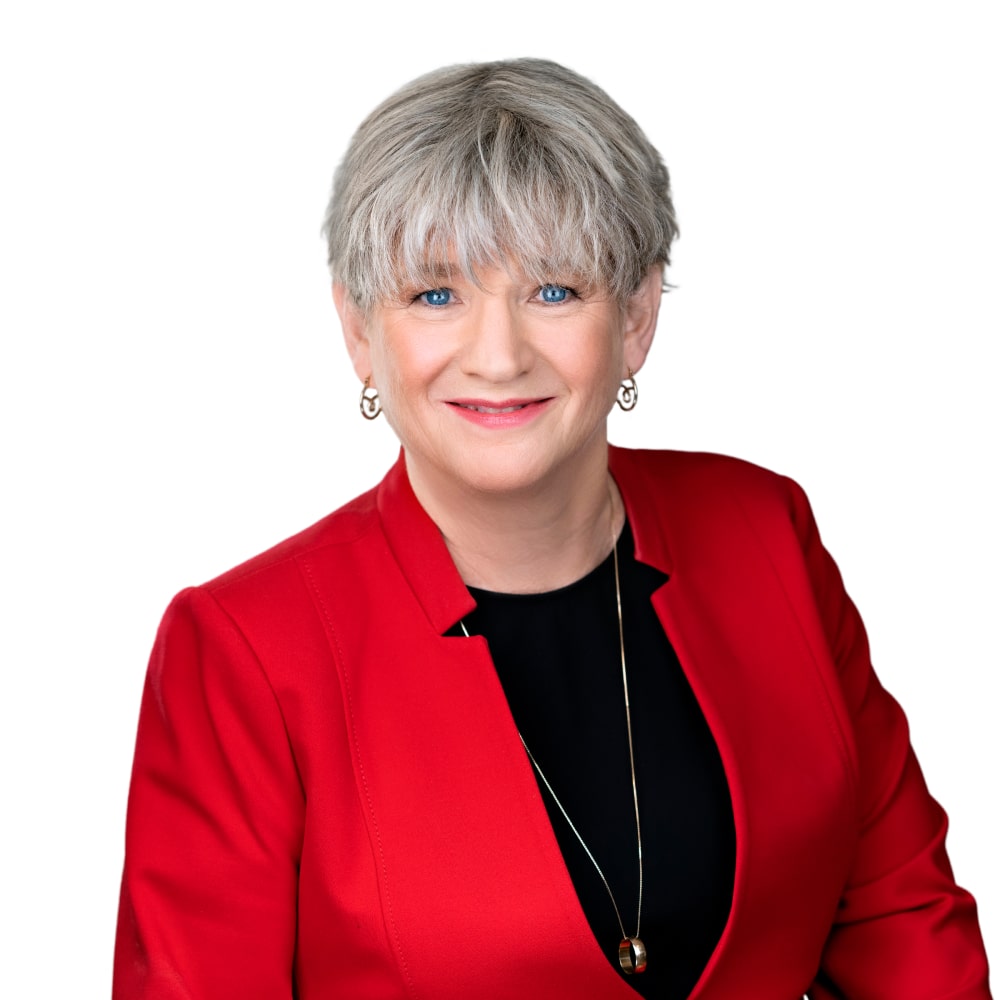