Turning raw, freshly-cut logs into boards of lumber may seem like an easy task, but there are actually a lot of steps involved in the process. From debarking and sawing the logs into manageable sizes to drying, planing, and grading the lumber, each stage requires precise techniques and careful monitoring to ensure the final product meets quality standards.
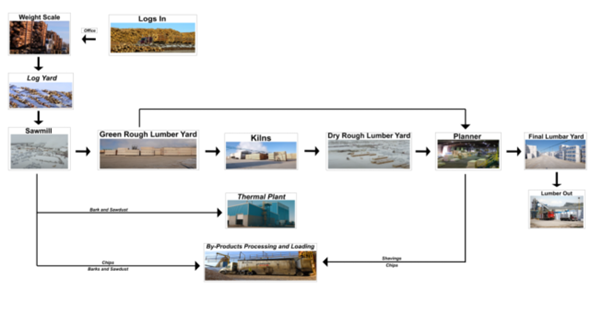
The log to lumber process
To start off, the logs are brought into the facility by the trucks, which are first weighed, then sent to the log yard. The logs are then stripped of their bark in a machine conveniently called the “debarker”. Following the removal of its bark, the logs are carefully directed into the primary conveyor system, where they undergo a sequence of critical procedures. The logs pass through a scanner that analyzes and determines the most optimal cuts to make on it, based on their dimensions and quality to maximize its value. These cuts are then made as it passes through machines. Some of the waste material which accumulates from the debarking and sawing processes are transferred onto the byproducts truck, while the rest is systematically gathered and repurposed at the thermal plant as a vital energy source for certain mill processes.
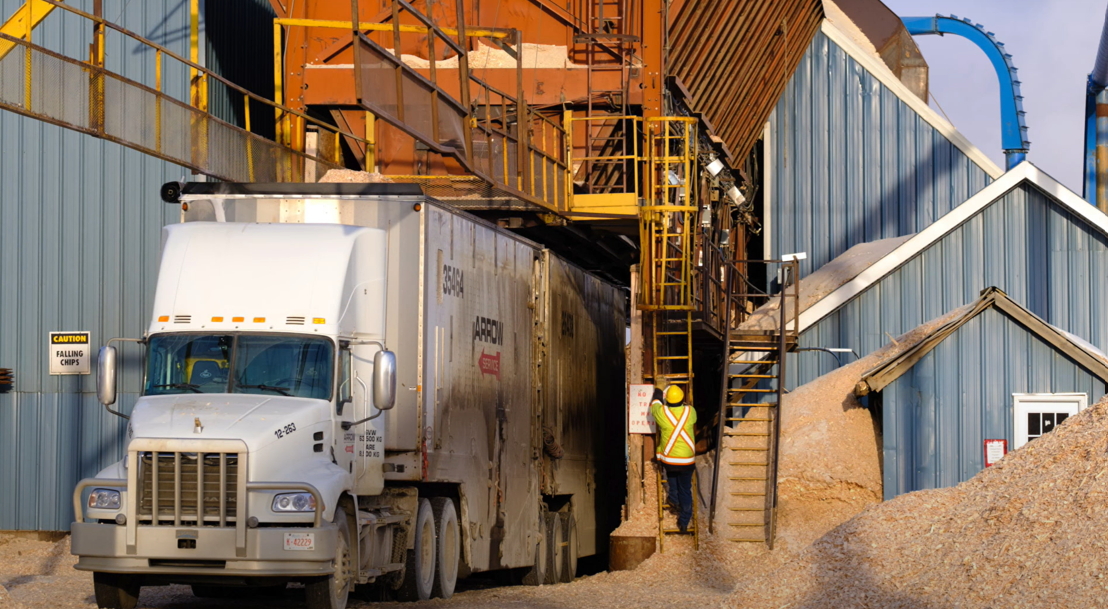
Chip byproduct truck being loaded
Once the logs are cut, they are transferred to the kiln, where they are heat-treated to remove moisture and eliminate pests and insects that may be present in the wood. The dried rough-lumber is then transferred to the planer mill, where they get stamped to receive their grading quality and is planed to achieve a smooth, uniform finish. This procedure not only enhances the aesthetic appeal of the wood but also prepares it for further applications in construction, furniture making, or other industries where quality and appearance are crucial.
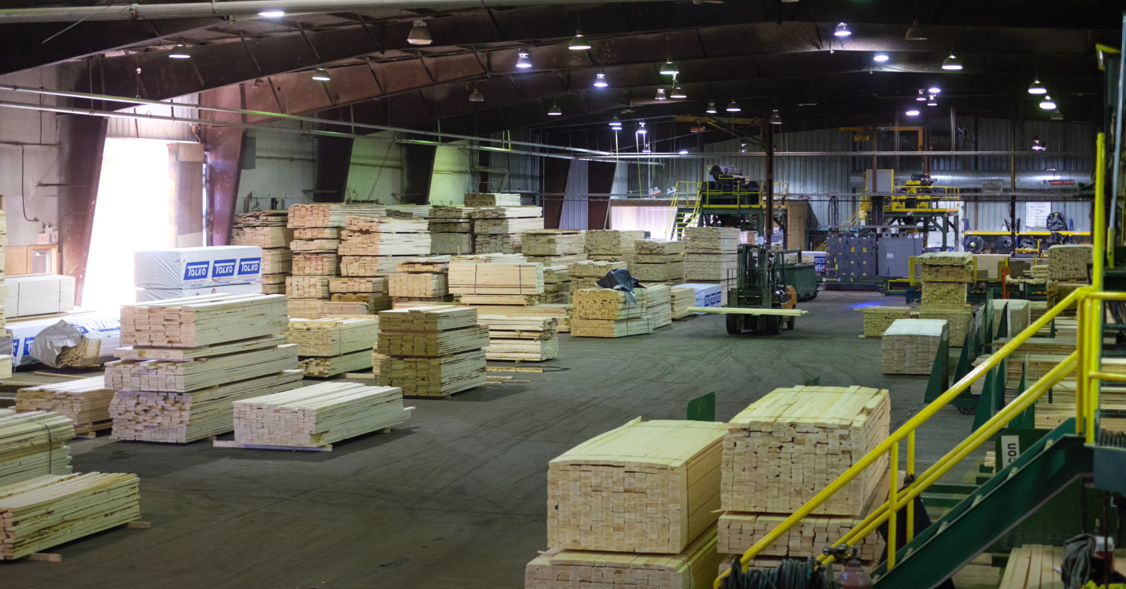
The planer lumber bundles
Throughout the process, various parameters and variables need to be thoroughly analyzed, monitored and controlled in order to ensure safety and quality of the lumber that is produced. This is where my role as the controls engineer comes in. As a controls engineer, my role revolves around designing and implementing systems that optimize the efficiency and reliability of every step in the mill's operations. This includes developing and fine-tuning automated processes that ensure smooth and seamless operation throughout the production cycle. By integrating advanced control systems and technologies, I aim to minimize downtime, maximize productivity, and maintain consistent quality standards.
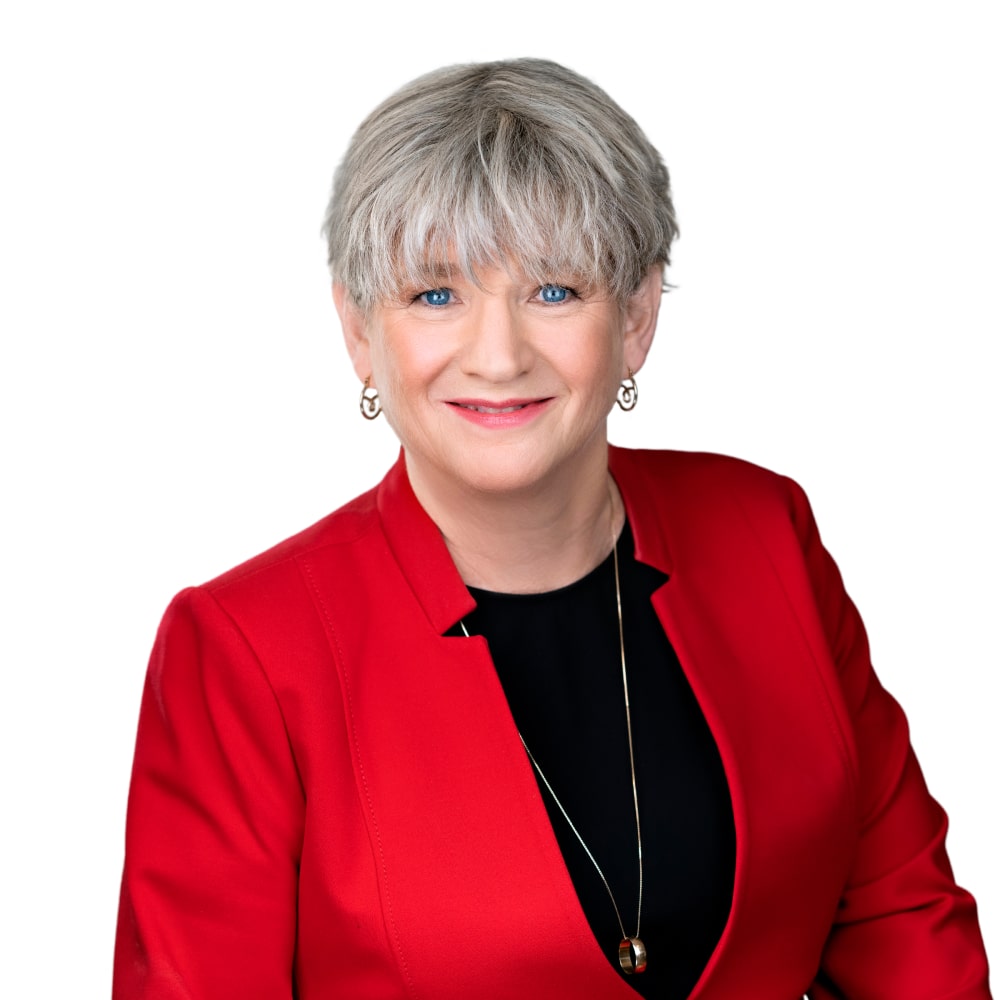