Hello to all of you,
Today, I'm going to show you the Kraft pulp process that we make at the Saint-Félicien mill. I also filmed a short video to show you the inside world of the mill. Finally, I'll tell you about the values that Resolute Forest Products promotes.
What is Fibrek?
Fibrek S.E.N.C., which has had Resolute Forest Products as its sole shareholder since June 2012, comprises three kraft pulp mills. Two of these mills are located in the United States (Fairmont in West Virginia and Menominee in Michigan) and make their pulp from recycled office paper.
The St-Félicien mill produces pulp using the kraft chemical process from northern softwood chips, mostly black spruce. 45% of its customers are Canadian pulp mills, 40% are American pulp mills and the remaining 15% is sent to Europe. The pulp is shipped to customers in bundles by truck and rail in Canada and the United States, and by ship for European customers.
Kraft pulp process
Receipt of chips
For pulp, it all starts with the wood. Logging companies harvest the trees and transport them to the sawmills. The residues are chipped. The chips are therefore by-products of the sawmills and become the raw material for the pulp mills. Although some pulp mills may receive wood in length, 100% of the wood received by the St-Félicien mill is in the form of chips. The mill receives approximately 180 truckloads of wood chips per day to meet its needs.
Screening
The chips should be passed through a series of sieves to remove sawdust and splinters. It is important to remove these items for the following reasons:
- They reduce the pulp yield;
- They reduce the mechanical strength of the dough;
- They increase the demand for chemicals.
Residues that are too small are purchased by another pulp mill that specializes in processing these residues.
Cooking and washing
After leaving the autoclave, the chips are transferred to the digester where they are brought into contact with the cooking liquor at a temperature of 160°C and under pressure. This atmosphere dissolves the lignin that holds the wood fibres together. When they leave the digester, the cooked chips dissociate into fibres because they are no longer bound together by the lignin. The pulp then passes through a pressurized diffuser and then into an atmospheric diffuser where it is washed. The purpose of washing is to recover the cooking liquor in the pulp by replacing it with cleaner wash water. The extracted black liquor, composed of sodium and sulphur, two essential products in the Kraft process, and dissolved lignin, is sent to a regeneration cycle where it recovers its initial chemical properties and is then sent back to the digester to cook more chips. The lignin will be burned and the energy released will be used to produce some of the steam needed for the mill's operations.
Skinning and sieving of the brown stock
After the enoueur, the pulp is directed to a series of sieves. Small particles such as uncooked fibre clusters, sand, rocks, etc. are thus removed to prevent them from contaminating the pulp.
After sieving, the pulp is passed through a rotary drum washer, called a thickener, where a final washing step will be performed. This equipment is also used to increase the consistency of the pulp to about 11% before it is stored in the sieved brown stock tank.
Bleaching
The bleaching stage involves taking the washed and sieved pulp and removing the more strongly bound lignin that was not removed in the cooking stage. Bleaching primarily addresses lignin since it is the main component responsible for the brown colour of the pulp. During this step, the pulp is sequentially contacted with three (3) steps of chlorine dioxide and two (2) steps of sodium hydroxide. The chlorine dioxide is used primarily for bleaching the pulp, while the sodium hydroxide is used primarily to dissolve the lignin in the pulp. Other chemicals such as oxygen and hydrogen peroxide are also added at certain stages of bleaching to achieve the desired 90% whiteness.
Dough machine
The dough is placed on a rotating cloth which allows the water to be removed by gravity and then by the vacuum created by vacuum boxes. The dough sheet then passes through 3 presses which transfer the water from the dough sheet to felts. Finally, the 96% air-dried degree of drying is achieved in a forced-air dryer. After leaving the dryer, the dough is cut into rectangular sheets. Approximately 400 sheets are stacked to form a bundle of about 250 kg. The bundles are then pressed, packed and sent for shipment. To ensure the traceability of the dough, each bundle is identified with a batch number and a bundle number.
Shipping
After leaving the packing line, the bales are either sent directly to wagons or stored for at least 24 hours (in winter) before being loaded onto trucks.
I am attaching my short film on a factory tour to see the manufacturing process:
We hope you enjoyed learning more about the Kraft pulp process and the company's values. See you in the future for more content!
Maïka Lambert
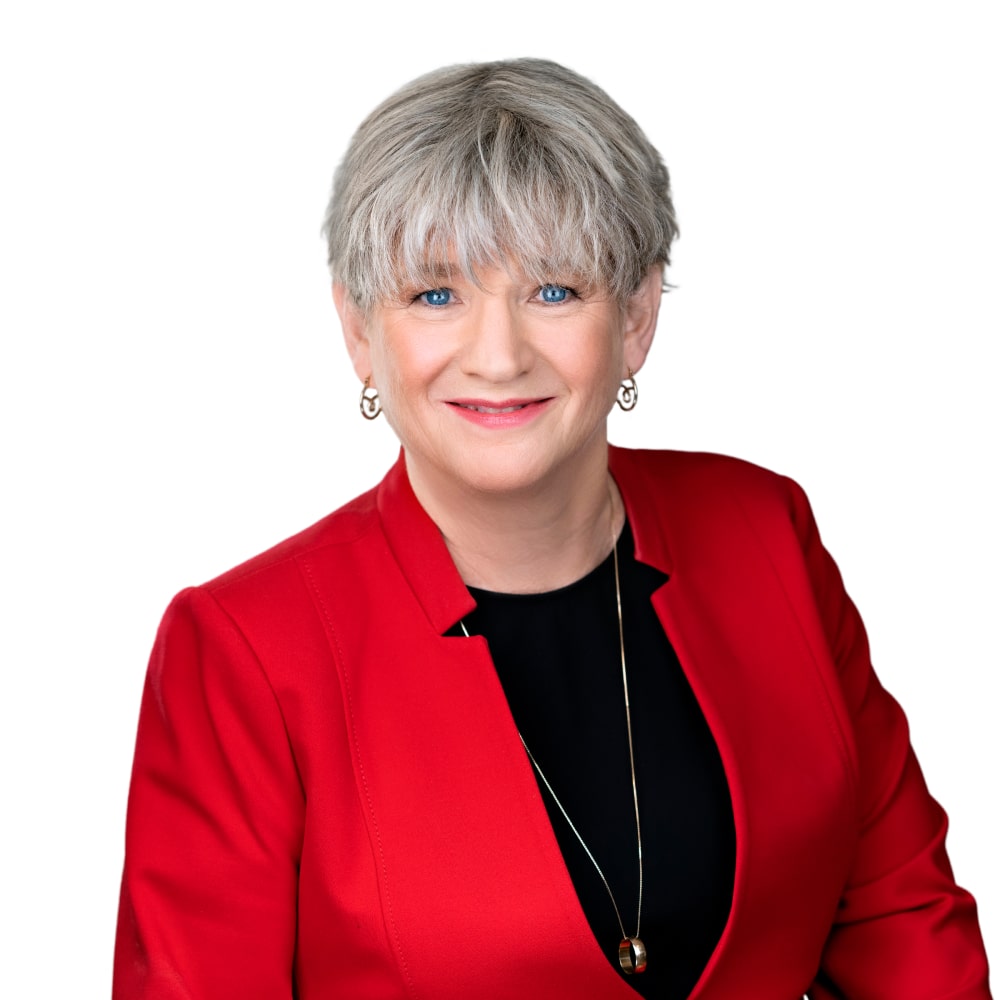