For my first shared content as a Green Dream intern, I would like to introduce myself and briefly explain the kraft pulping process that takes place just outside my office.
My name is Marlies, and I just finished my second year of chemical engineering at Lakehead University. This summer, I’m working as a chemical engineering student on the Fiber Line at the Resolute Forest Products Kraft Pulp Mill in Thunder Bay, ON.
At the kraft mill, various departments collaborate to transform woodchips into the pulp that we sell. The two major groups are the Fiber Line and the Utilities Department. The Fiber Line handles the physical transformation of wood chips into pulp and comprises fiber handling, the digester, the bleach plant, and the machine room. On the other hand, the Utilities Department manages the liquor cycle in the kraft process and includes chemical recovery, recausticizing, as well as steam and power generation.
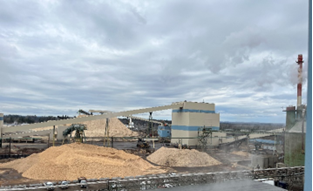
Now I’m going to quickly walk you through the fiber line so you can get an idea of where I fit in at the mill.
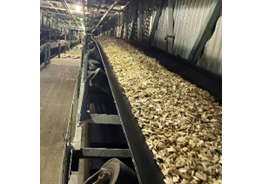
The process starts with woodchips collected in large piles on the mill property, which are then fed onto a conveyor belt leading to the screenhouse. Here, the woodchips pass through several screens that filter out oversized and undersized chips. Afterward, the chips travel up another conveyor belt and enter the digester after pre-conditioning in the chip bin. The digester is an enormous 10-story-tall pressure vessel that operates at extremely high pressures and temperatures.
The digester employs white liquor, containing sodium hydroxide (NaOH) and sodium sulfide (Na2S), to break down the wood chips. This process solubilizes the lignin, which refers to the colored macromolecules in wood that act as glue to hold the fibers together. Consequently, the chemical reactions in the digester transform the white liquor into black liquor, which contains the products of the reactions. The black liquor is then sent to the Utilities Department for chemical recovery, where it goes through a series of steps to be regenerated back into white liquor.
Once the chips leave the digester, they are no longer chips, but partially processed pulp. The pulp then goes through a series of washing stages, more screens, and thickeners before it reaches the bleach plant.
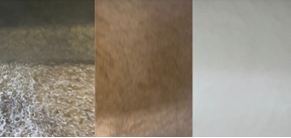
The bleach plant consists of several stages that further break down and remove the lignin from the pulp while simultaneously brightening it. Chemicals that are added in the bleaching process include chlorine dioxide (ClO2), caustic (NaOH) and oxygen (O2). After each stage in the bleach plant, the pulp is thoroughly washed. If you look inside the washers in order (15, 25, 35, 45, and 55) you are able to clearly see the pulp get brighter and brighter with each stage
Finally, once the pulp is bleached it is sent to the machine room. Starting at the wet end, the pulp slurry from the bleach plant is diluted with water to a 1-2% consistency. This means it’s almost completely water! The slurry is pumped to the pressurized headbox and exits onto the forming board, consequently forming a sheet of pulp on the wire of the fourdrinier. Ensuring controlled stock characteristics onto the fourdrinier is crucial to achieve the desired basis weight and air dry of the pulp. The water begins to drain through the bottom of the wire immediately due to gravity and vacuums created in sections of the fourdrinier. The wet sheet of pulp then goes through a series of presses and more vacuums which work to remove as much water as possible before the sheet goes into the dryer. The start of the dryer marks the beginning of the dry end. Once the sheet passes through the dryer, it goes to the cutter and layboy where it is sliced into smaller, more manageable sheets that are then stacked, pressed into bales, packaged, labelled, and eventually shipped to customers.
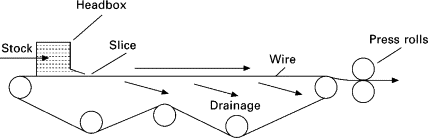
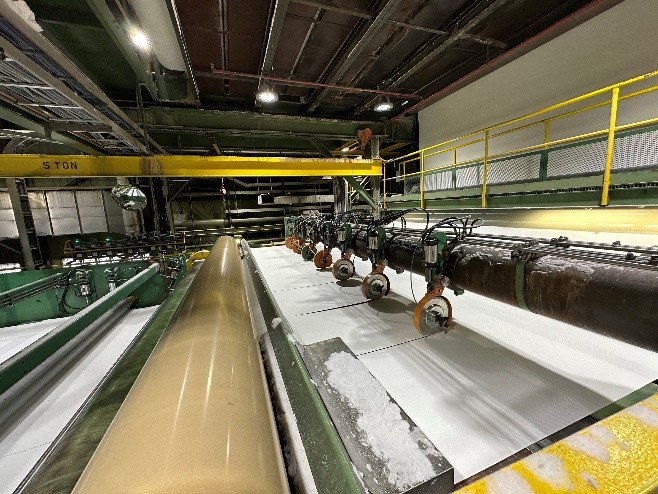
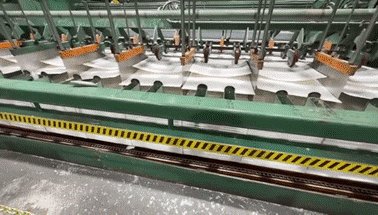
Although this explanation is a simple overview, it gives an idea of just how many steps there are in the process. There are many, many, other pieces of equipment, processes, and chemicals not mentioned above that all play a very important part in producing the finished product. As my summer at the mill continues, I’m looking forward to continuing to learn about this fascinating process and all the intricate details involved.
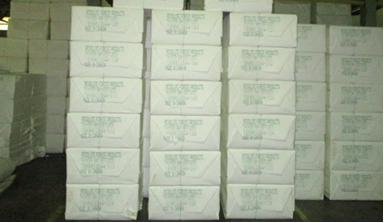
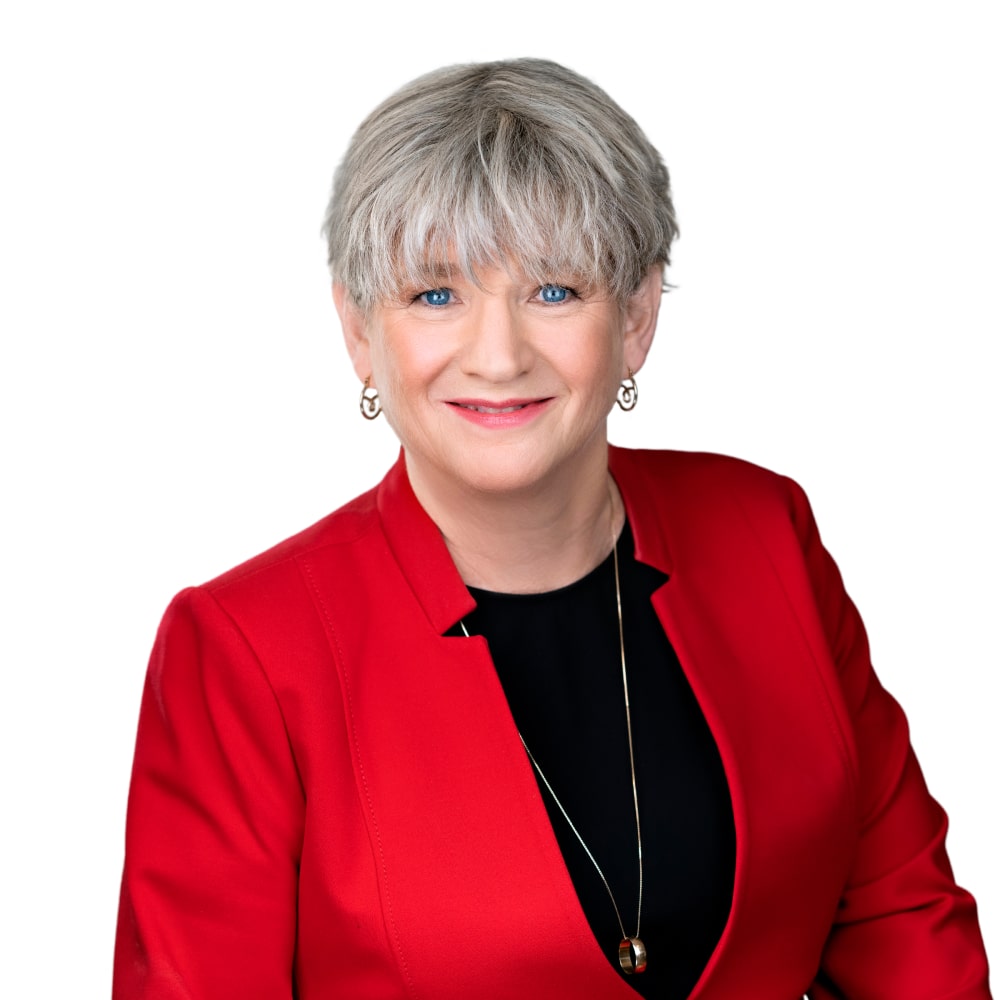