Hello!
My name is Victoria Carlyle and I am very excited to be a part of FPAC’s Green Dream Internship program! I am spending my summer as a “Chemical Engineering Student” at Resolute Forest Products’ Kraft Pulp Mill in Thunder Bay, ON. My summer position and my educational background is all STEM heavy and technical, so I figured a good first entry would be a brief explanation of how the process at the mill works so we can better understand how I fit into it.
There are 3 main components to the process outlined in the map attached:
- The Fibre Line (produces pulp) outlined in brown
- The Liquor Cycle (produces by-products of Turpentine and Tall Oil) outlined in purple
- The Power Line (produces renewable electricity using biomass) outlined in red
The Fibre Line
The Fibre Line is the main line of the process that produces pulp. Wood chips are first screened by size and density to remove any large pieces and rocks before being sent to the digester. Digesting the chips with white liquor removes the lignin present in the wood. Lignin is the compound that gives wood its rigidity. Coming out of the digester, the wood chips now have a mushy, pulp consistency. This pulp is then washed and bleached several times to remove residual liquor and increase the brightness of the eventual product. Finally, at the pulp machine, a thin layer of pulp solution is vacuum dried and cut to create sheets of pulp to be sold as the final product! Market Pulp can be further manufactured into many things such as tissues, paper towels and printing/writing papers.
The Liquor Cycle
The Liquor Cycle is a chemical loop that allows used liquor coming out of the digester to be reused again and again. The type of liquor (White, Black or Green) is named for the liquor colour at its current stage in the process. Going into the digester, the liquor chemistry is NaOH and NaS2 which gives the liquor a white colour. Coming out of the digester, the liquor chemistry is full of various heavy organic compounds that have been removed from the wood chips, giving it a black colour. The Evaporators strengthen the concentration of solids in the black liquor by removing water. This is where the liquor becomes “weak” in black colour (and solids concentration) versus “strong” in black colour (and solids concentration). After the evaporators, strong black liquor is fired into the Recovery Boiler where the heavy organic compounds are burned off, leaving a liquor chemistry of Na2CO3 and NaS2 which appears green. At this point in the process it is called green liquor. The final step from green liquor back to white liquor requires the Na2CO3 to become NaOH. This is accomplished using a Recausticizing reaction with lime and water (which have their own recycling loop for re-use). Exiting Recaust, the liquor is white again and ready to be used in the digester. This chemical recycling loop saves the cost of having to constantly use fresh digesting agents, and ensures used liquor and rich organics aren’t wasted through disposal. There are also two valuable by-products that come out of the liquor cycle; black liquor contains materials that can be separated to produce Turpentine and Tall Oil. Both can be sold as additional products. Turpentine can be used as an industrial solvent and Tall Oil can be further refined to make emulsions, lubricants and soaps.
The Power Line
Although we do not use bark from the trees to produce pulp, it can be used to create electricity! Bark undergoes a screening process to remove dirt and rocks and then is combined with sludge from water effluent treatment to create biomass fuel. Burning biomass in a Power Boiler releases energy that we capture as steam. This steam is then fed through our turbines to produce electricity. This electricity can then be used internally, or sold to the grid for commercial use.
In my opinion, the most interesting part of the overall process are the things going on outside of the main fiber line. Pulp is the main product produced in our Kraft Mill, but there is also a lot going on behind the scenes to increase the profitability and efficiency of the entire process. Going into my placement with Resolute, I didn’t know anything about the forest product industry; the process seemed impossibly large and complicated. Fortunately, I am working with some very knowledgeable people and on my first day I was given a simple flow chart – much like this one. I still refer back to it. Chemical processes (and science in general) can seem very daunting, but everything can be broken down into simpler, more manageable pieces. I hope you learned a little bit about the pulp process and I look forward to sharing more about my experience with you in the future!
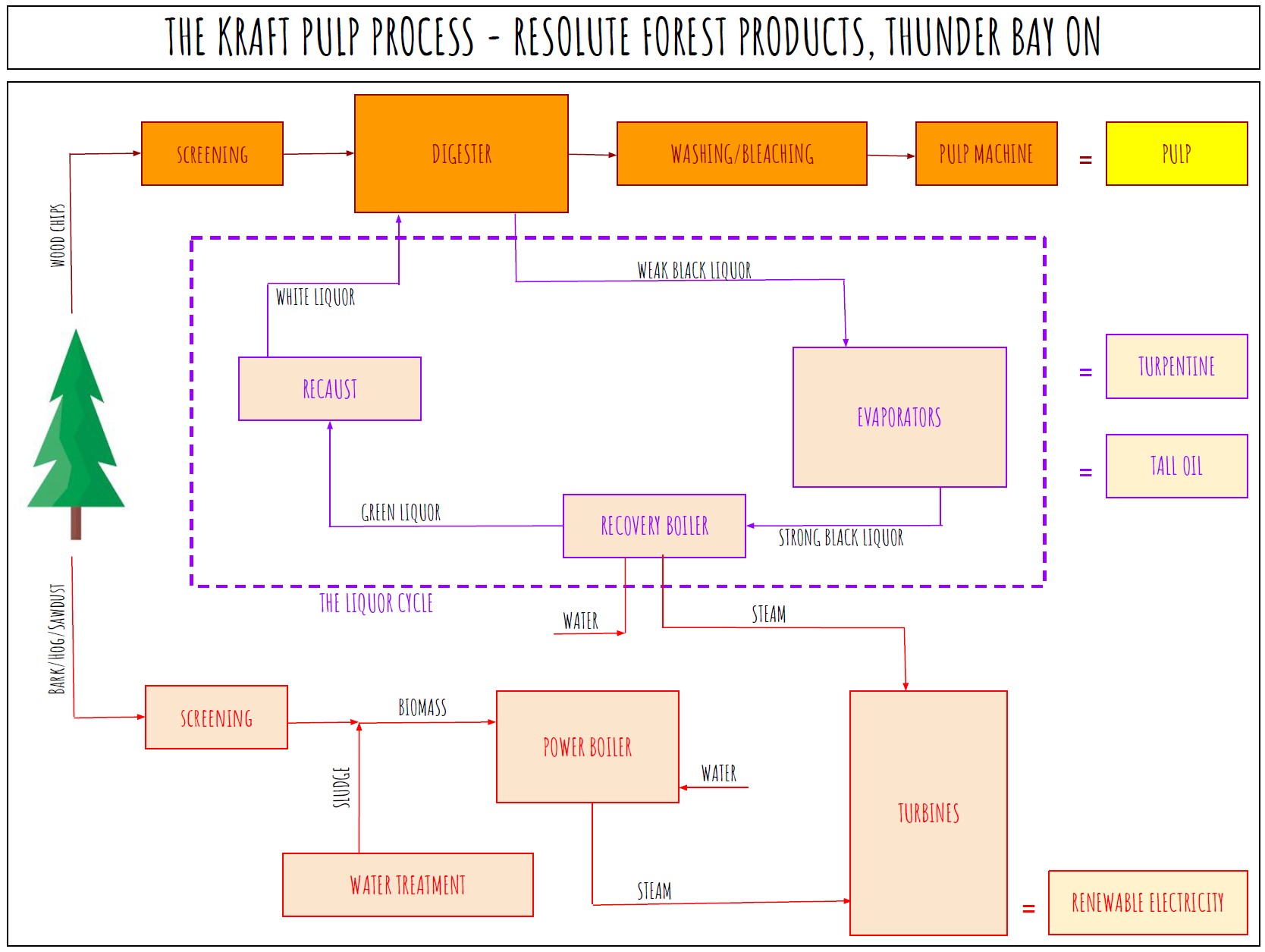
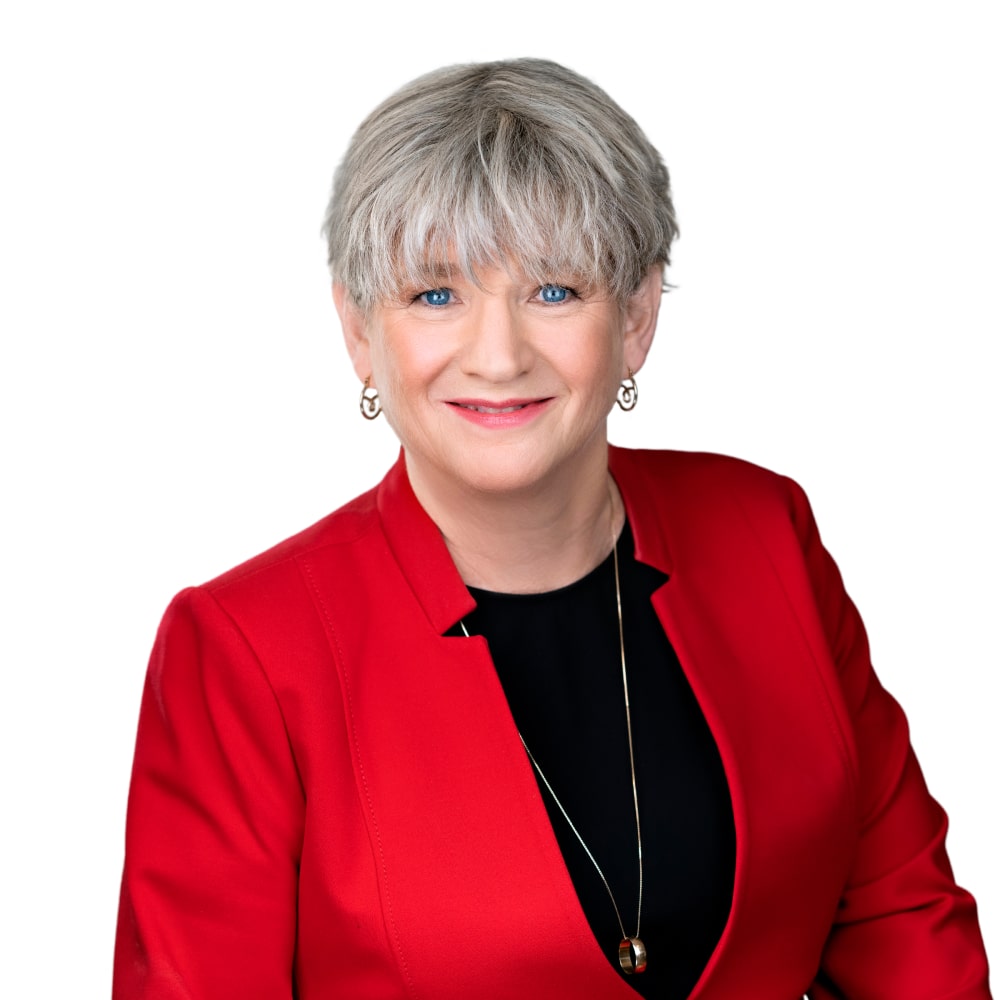