As the end of my short blogging career is coming to an end, I would like to talk about some of my favorite parts of working for Tolko, and specifically at the Athabasca OSB division. There are many things which have made my work term at Tolko very enjoyable, and to summarize them I have used the six core values at Tolko to explain my favorite parts. I have been fortunate enough to have worked for several companies during my summers in high school and university before coming to work for Tolko for my first official co-op in the Wood Products Processing Program at UBC. This has given me some experience in other industrial settings, and it has also allowed me to see what Tolko does better than some of the other companies that I previously worked for.
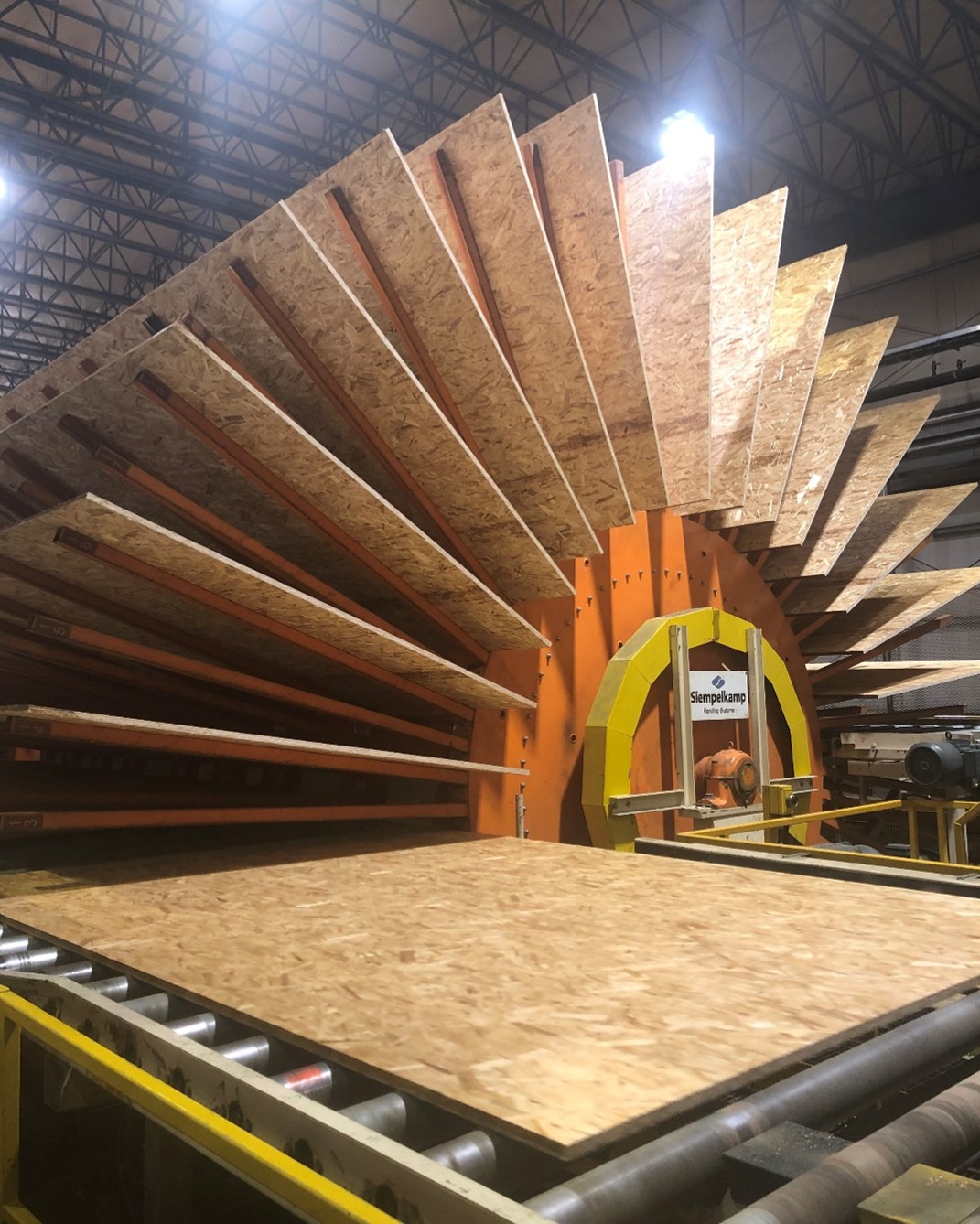
The first thing that I have enjoyed about working for Tolko is their value placed on safety. They have done such a good job at training us that whenever a task needs to be completed, the question about how to complete the task safely is the first thing that comes into mind. Once all the risks are evaluated, steps are made to eliminate the risks to make it safer for employees to complete the required work. When all the employees think about how they can be safe in their work, it reduces the number of accidents that happen, and everyone feels safer at work.
The next thing that I think Tolko does very well and I really enjoyed is the respect shown to each employee. Everyone is treated fairly no matter your background or ethnicity. Not only that, while working here, Tolko has done a very good job of giving people the opportunity to voice their opinions about different issues. Their opinions and ideas are all listened to in a respectful manner, and if something indeed needs to change and it is a doable fix, an effort is made to improve the situation.
I have also noticed that Tolko focuses on improving both the individual employees and the mill itself. As I mentioned in the previous paragraph, employees are given opportunities to provide suggestions about different issues, and if their idea is reasonable then Tolko works to improve the process. There is also a large push at Tolko to train employees to be competent on as many pieces of machinery and processes as possible to build their employees’ skills and to make everyone more versatile in their abilities. This includes providing training for various pieces of equipment if interest is shown by an individual, a pay for skills system which provides a monetary value to employees for the more jobs they are competently able to do, and a large push to hire internally for supervisory roles. By training employees for a wide variety of tasks, it not only makes the employees feel like they are valued, but it also helps the company because their personnel are much more flexible if certain areas of the mill are struggling. I personally experienced this while working there because I was trained on running all the lab equipment as well as machinery such as forklifts, table saws, and even training to get my official lab technician certificate.
While working with the technical department at Tolko I have seen the firsthand commitment to integrity. The technical department supervises the quality of the finished product that is produced, and we ensure that all the product which we produce meets or exceeds the quality requirements set out by our customers and grading agency. While working for Tolko this summer I have helped with ensuring that the board dimensions are in tolerance, that the regular board testing meets the requirements, and that the overall board quality is something we are proud of making. By producing something that is consistently a quality product, this builds relationships with customers because they trust they are receiving a product that is easy to work with and has no issues. Conducting testing was a large part of my responsibilities as a quality student, and I really enjoyed working with the various departments to do the testing and fix any issues when they arose.
While I was going through the onboarding process for Tolko, many of the supervisors which presented said to stop in their offices anytime their door is open to talk about any issues or questions we may have. I was skeptical that this was the case, but the longer I work here the more I appreciate the openness that exists with being able to walk into anyone’s office and talk about any concerns I have. Not only will they listen to any concerns, but they will try and help you if your request is reasonable.
Through programs such as lean manufacturing and production trials, Tolko continues to improve its process by using its raw materials more efficiently and by eliminating unnecessary processes which waste time and material. I have enjoyed learning about and helping implement these changes because they improve Tolko’s bottom line and therefore increase its profit. By implementing lean manufacturing and conducting trials it has also shown to me the importance they have on allowing companies like Tolko to be competitive and innovative in the manufactured wood industry.
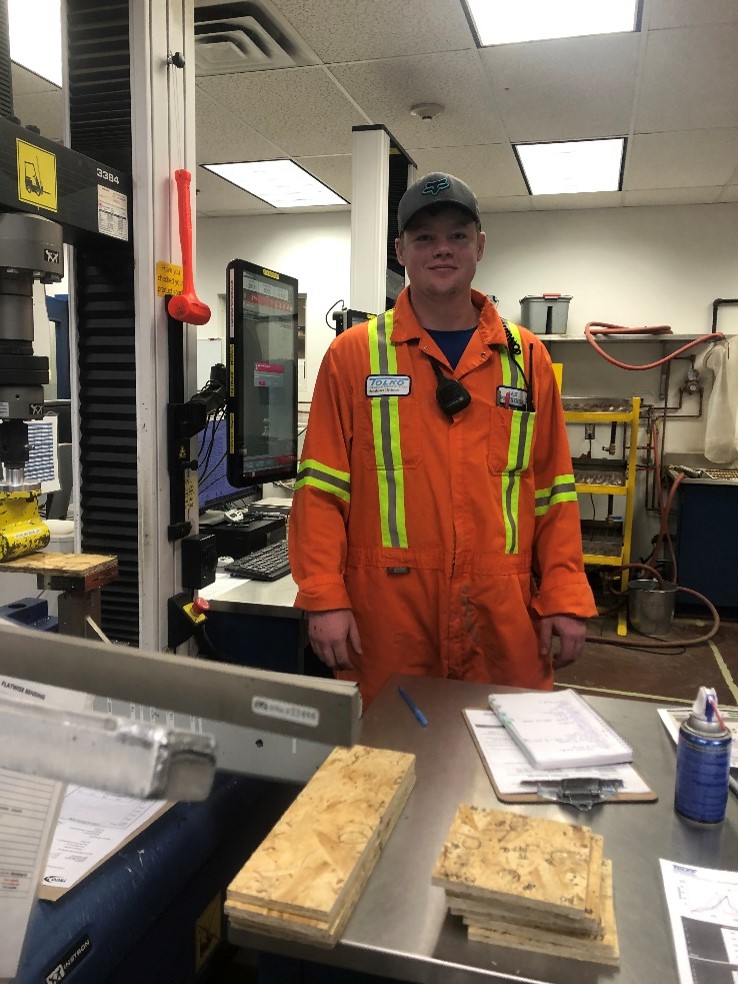
The final thing I have enjoyed working for Tolko is the people. This is not exactly one of their values, but I decided that I should include it. Even though many of my questions I asked made me out to be an idiot, everyone was always willing to explain things and their purpose. In the hallways people say good morning and anytime I needed help people were willing to take time out of their day and help. I spent most of my time working in the lab where everyone was extremely friendly and helpful as I learned. Overall, I have had an extremely good experience working for Tolko and am very grateful for all the connections I have made here and the things I have learned from working there.
Have a great week,
Ian Penninga
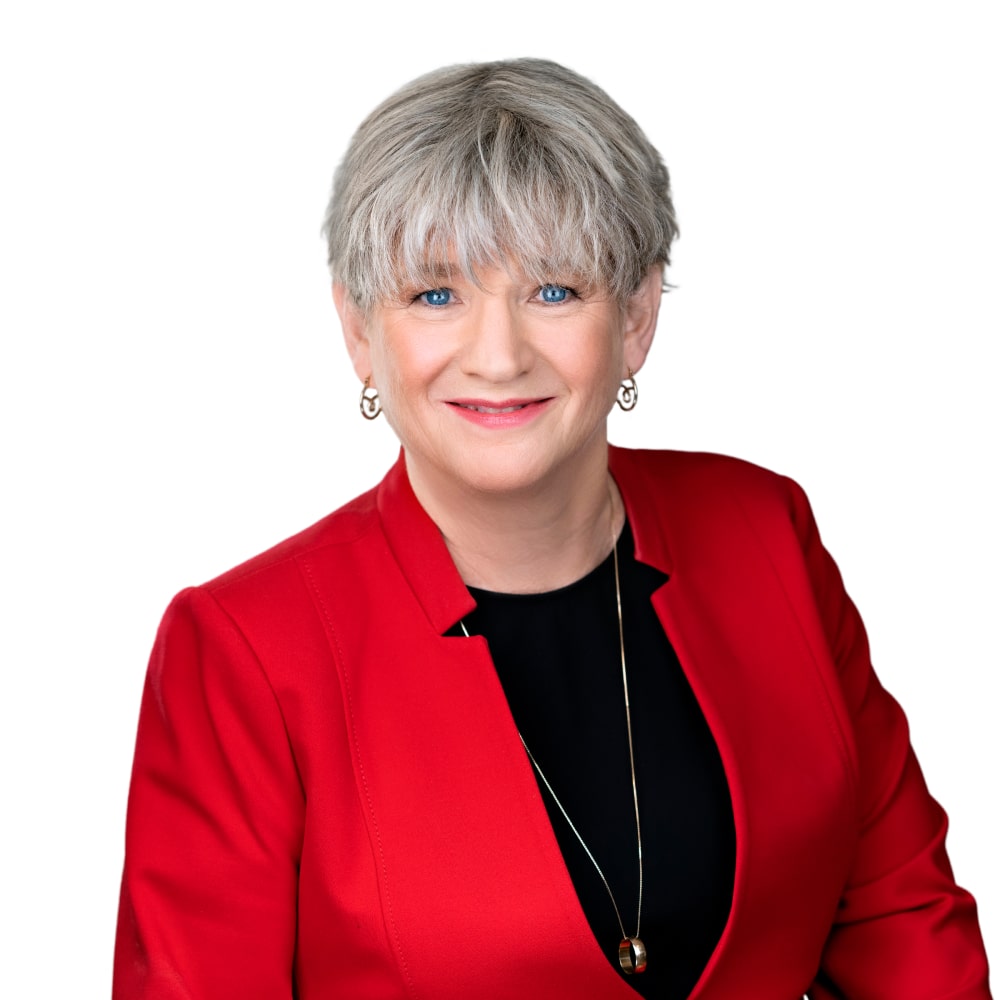